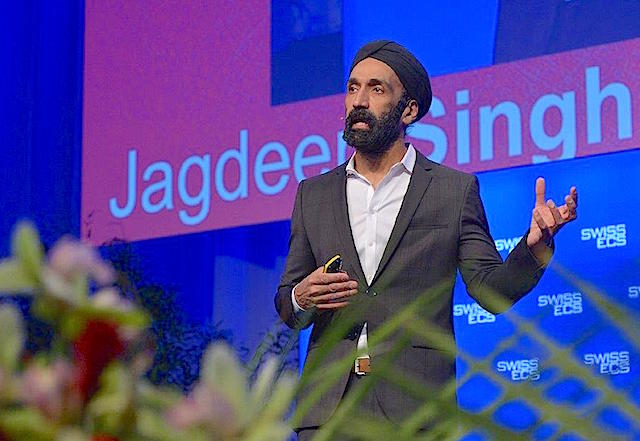
US start-up QuantumScape (its largest shareholder is Volkswagen) has said it’s developed a solid-state battery based on a deceptively simple idea.
Instead of a conventional liquid electrolyte – the stuff that ferries lithium ions between electrodes – it uses a solid eloctrolyte. Also, the battery’s negative terminal, called its anode, is made from pure lithium metal.
QuantumScape’s co-founder and CEO Jagdeep Singh (above) has just released test results. Singh says the flexible battery – roughly the size of a playing card – resolved all of the core challenges that have plagued solid-state batteries in the past, such as incredibly short lifetimes and slow charging rate.
According to QuantumScape’s data, its cell (below) can charge to 80 per cent of capacity in 15 minutes, it retains more than 80 per cent of its capacity after 800 charging cycles, it’s noncombustible, and it has a volumetric energy density of more than 1000 watt-hours per litre at the cell level, nearly double the energy density of top-shelf lithium-ion cells.
Meantime, it’s a problem that doesn’t exist on a large scale in New Zealand yet – how to recycle spent lithium-ion batteries in use in current electric vehicles (EVs).
But it’s one the Government must grab hold of as it moves towards electrifying its fleet of vehicles and telling Kiwis in general to get into EVs.
A far-sighted approach for recycling batteries is important. As more batteries are manufactured to keep up with the increasing demand for EVs, the recovery of the critical materials in these batteries will be vital to create a circular, sustainable industry and to manage waste.
The International Energy Agency predicts an 800 per cent increase in the number of EVs over the next decade, each car packed with thousands of cells, each cell with a use-by date.
Global environmental agencies say there’s an e-waste timebomb in the making, and cracking lithium-ion recycling is the only way to defuse it.
In other words, how to cook down lithium-ion batteries to recover the raw materials – nickel, cobalt, manganese, copper, aluminum, graphite, lithium – needed to make new batteries.
Recycling of lithium-ion batteries in New Zealand is pretty much limited only to the dismantling of the battery packs themselves. Toyota/Lexus NZ, for instance, sends its spent hybrid batteries to Auckland company Upcycle. So does Audi.
Upcycle recycles the plastic and metal components but sends the essential battery cells to the Kobar company’s recycling plant in South Korea. Toyota is building its own battery-recycling centre in Thailand.
Toyota, Audi, Tesla, BMW and China’s LDV are among the 85 members of the Battery Industry Group (BIG), a collective set up in 2018 to “deliver practical and innovative solutions to help NZ safely manage its large batteries.”
It’s an alphabet soup of titles. One of BIG’s working groups is BUG (Battery User Group). BIH (Battery Innovation Hub) has a role, so too has SL&G (Safety and Logistics Group) and the SMRANZ (Scrap Metal Recyclers Association of NZ). BIG is reportedly waiting for funding from the Ministry of the Environment (MfE) and the EECA (Energy Efficiency and Conservation Authority). When that arrives BIG can presumably work closer with BUG. Or BUG with BIG.
Whatever BIG and BUG’s end game, no battery recycling method exists which is both efficient and profitable enough to be sustainable. Not in NZ nor overseas.
At the end of its life, a lithium-ion battery still retains around 80 per cent of its charge, not enough to run an EV but enough for different applications, like energy storage.
Much of the recycling that does take place today is done through a combination of pyrometallurgy and hydrometallurgy. Pyrometallurgy involves burning the batteries to remove unwanted organic materials and plastics. This method leaves the recycler with just a fraction of the original material. The rest goes to the slag.
Canadian company Li-Cycle bills itself as the largest lithium-ion recycler in North America. It skips the pyro step entirely. First, it drops the batteries into a vat that simultaneously discharges and shreds them. Next the compound goes through a chemical bath to unlock individual metals. The process converts almost everything back into a usable raw material.
“Historically, batteries were viewed as waste, and we seek to turn that on its head by focusing on them as a resource,” said Li-Cycle co-founder Tim Johnston (above right). “We don’t produce any meaningful amounts of waste. We don’t produce any meaningful amount of air emissions, we don’t produce any waste water, and everything is done at a low temperature. The footprint is very small.”