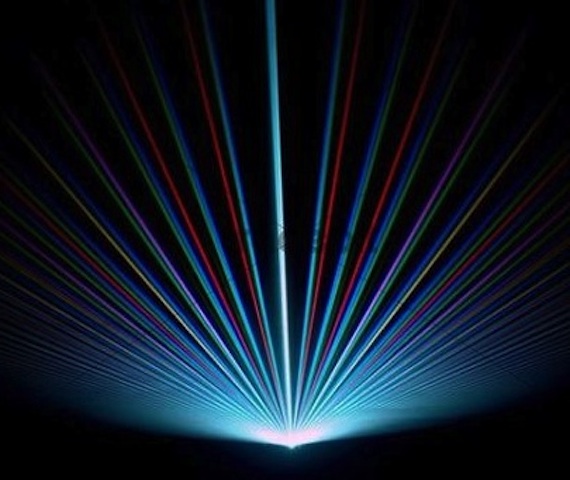
Lasers might replace spark plugs in petrol engines to improve their efficiency, thanks to a team of Japan-based researchers.
Compared with conventional spark plugs, which ignite the air/fuel mixture and create a flame front that spreads throughout the combustion chamber to force the piston downwards, laser beams can be accurately focused to start the combustion at the most efficient point.
The researchers from Japan’s National Institutes of Natural Sciences claim that because the flame front generated by a spark plug travels across the relatively cool surfaces of the combustion chamber as it starts to expand, some of its energy is lost.
A laser can avoid this by focussing the beam into the centre of the combustion chamber. Team member Takunori Taira said this caused the flame front to expand more symmetrically and up to three times faster than it would if ignited by a spark plug.
In addition, several beams can be used simultaneously for an even faster, more complete burn and lasers can be more precisely timed than spark plugs – in nanoseconds as opposed to milliseconds – resulting in more efficient combustion.
Although spark plugs have the ability to ignite lean fuel/air mixtures, the increased spark energy required causes the spark plug electrodes to degrade rapidly.
Lasers are able to inject enough energy to the combustion chamber to ignite a lean fuel/air mixture without such wear and tear.
The faster, more accurate and leaner combustion made possible by laser ignition results in improved fuel economy and reduced emissions – particularly NOx, which contributes to smog.
The research was funded by the Japan Science and Technical Agency with support from Denso, a major vehicle component manufacturer and part of the Toyota Group.
The team is working with a spark-plug company and Denso to explore the possibilities of bringing the technology to market.
Using lasers to replace the spark plug – which has been around since 1860 and first made commercially viable by Robert Bosch in 1898 – is not a new idea.
In 2006, Colorado State University filed a US patent for a special type of optical fibre that could withstand the high levels of energy required to create a spark in an internal combustion engine.
In 2009, Liverpool University in Britain, in collaboration with Ford, did research into using laser-to-power combustion in mass-produced petrol engines.
The researchers ran a four-cylinder engine using laser ignition, recording smoother running and reduced exhaust emissions.
However, they met problems delivering the beam to what they called the optical spark plug via fibre-optics and could only use it by aiming the separate laser unit’s beam directly into the engine – making it impractical for commercial use.
Taira’s Japan-based team was well aware of the limitations faced by other researchers into the field of laser ignition.
“In the past, lasers that could meet requirements were limited to basic research because they were big, inefficient, and unstable,” he said.
As the Liverpool and Colorado Universities found, the lasers could not be located away from the engine because their powerful beams would destroy any optical fibres that delivered light to the cylinders.
Taira’s team has circumvented the problems by using ceramics to make a powerful composite laser just 9mm wide by 11mm long that generates two beams that can simultaneously start combustion in separate areas of the combustion chamber.
The benefit of using ceramics, other than their effectiveness in dissipating the engine’s heat, is that they are easier to tune optically than conventionally-used crystals, while being stronger and more durable.
Although the laser is not strong enough to ignite lean fuel/air mixtures with a single pulse, it overcomes this by using several 800 picosecond (a picosecond is a trillionth of a second) pulses to inject enough energy to the combustion chamber for ignition.